VIP member
Vibration grinder ZM vibration grinder Henan Weicheng Machinery
1、 Overview: ZM vibration mill uses the excitation torque generated by the exciter to cause high-frequency vibration of the cylinder (with a vibration
Product details

1、 Overview:
The ZM vibration mill uses the excitation torque generated by the exciter to cause high-frequency vibration of the cylinder (with a vibration intensity of 3-10g, where g is the acceleration due to gravity),By relying on the strong impact and grinding effect of the grinding medium inside the vibration grinding cylinder, the material is crushed; At present, the 2ZM series vibration mills produced by our factory are a new generation of products developed and researched based on absorbing advanced technology and experience at home and abroad.
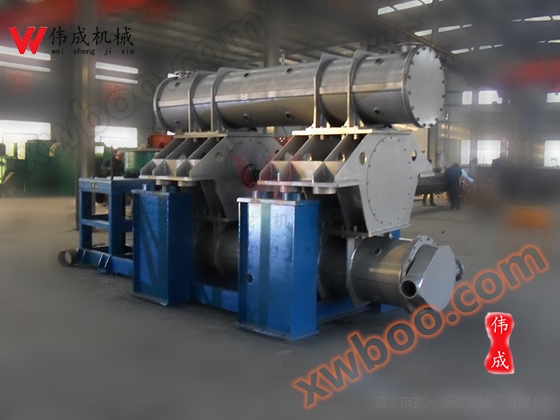
2、 Main features and applications
1. Characteristics
Compared with ball mills, this machine has the following significant characteristics:
3. Small footprint, easy to install and isolate
4. Low energy consumption per unit output
5. Concentrated grinding particle size
6. Easy to operate and control
7. The whole machine is lightweight, with a high ratio of output to weight
8. Low noise
9. Simple process and easy maintenance
10. Easy replacement of lining plates and media
11. Not affected by the optimal acceleration index of 0.8g, the grinding medium is small and the unit grinding surface changes greatly.
2. Purpose:
This mill is a small and medium-sized non flammable and explosive material grinding equipment, mainly used for fine and ultrafine material grinding in industries such as metallurgy, mining, building materials, refractory materials, abrasives, glass, ceramics, etc. It is widely used as a raw material for ultrafine processing in the production of chemical dyes, special ceramics, grinding metallurgy, and advanced refractory materials.
3、 Technical performance and main parameters

4、 Structure and working principle

As shown in the table, this machine is mainly composed of a chassis, a body bracket, a soundproof cover, a body, a grinding cylinder, an exciter, a lining plate, an elastic support, a grinding medium, and a drive motor.
1. The chassis is elastically supported to lift the body and maintain the flexible connection distance between the driving motor and the vibrating body unchanged.
2. The soundproof cover is used to block the noise emitted by the grinder during operation, in order to reduce the impact of noise on the entire work area.
3. The body is fastened with a grinding cylinder and equipped with an exciter.
4. The grinding cylinder is the working body of the vibrating mill, used to hold the grinding medium and abrasive.
5. The exciter is used to convert the rotational torque of the motor into the periodic vibration of the mill.
6. The lining plate is tightly attached to the inner wall of the grinding cylinder to protect it. When vibrating and grinding materials inside the grinding cylinder, there is also significant wear on the inner wall of the grinding cylinder. Installing an easily replaceable lining plate inside the grinding cylinder can improve the service life of the entire machine.
7. Elastic support is used to keep the grinder body in an elastic state and basically isolate the vibration impact on the base when the body vibrates.
8. The grinding medium is the grinding body of the grinder, used for impact grinding of materials.
9. Drive the motor to provide energy for the vibration grinding of the mill.
Connect the power supply and drive the motor to rotate the exciter through a flexible coupling, generating sufficient excitation force to cause the mill body to enter a cyclic vibration state. The oscillation force is continuously transmitted to all the materials loaded into the grinding cylinder (i.e. the medium and the ground material), and the ground material is finely ground by the mutual impact between the ground medium and the ground material.
5、 Scope and form of use
The ZM series grinder can vibrate grind a variety of materials, and its processed finished product particle size can range from medium particle size (0.3mm) to finer particle size (0.075mm). Its production capacity is high, and the grinding processing effect can be the ideal equipment at home and abroad.
The usage form and scope of each form of ZM series vibration grinder:
1. Series form
As shown in Figure 18-2, after the grinding of the material from the first cylinder is completed, it enters the second cylinder for further grinding. This form is suitable for harder materials and products that require the finest particle size.
2. Parallel use
As shown in Figure 18-3, feed and discharge the two cylinders separately. Compared with the series connection form, the vibration grinding distance of the material in the cylinder is halved, and the vibration grinding time is also halved. The grinding effect of the material is weakened, and the processing capacity of the machine is improved, which is suitable for non hard materials and non finest particle processing situations.
3. Intermediate feed
As shown in Figure 18-4, feed the two vibration grinding cylinders separately from the middle, and discharge each cylinder from both ends. Compared with the parallel form, the vibration grinding distance of the material inside the vibration grinding cylinder is halved, and the vibration grinding time is shorter. This method is suitable for high productivity and coarse-grained material production.
4. Dry vibration grinding
When the moisture content of the material is less than 5%, it is suitable for vibration grinding in a fully dry state. At this time, the vibration grinding temperature is high. If the temperature resistance of the vibration grinding material is poor, a water jacket needs to be added to the grinding cylinder, and circulating water needs to be used to cool it down through the grinding cylinder wall.
5. Wet vibration grinding
If the moisture content of the material is greater than 40%, it can directly enter the cylinder for vibration grinding, which is called wet vibration grinding.
6. Closed circuit method
The above mentioned methods all involve feeding and discharging at the same time. If ultra fine particle size needs to be obtained, the discharge port of the cylinder can be blocked, allowing the material to be continuously vibrated and ground in the cylinder for several hours or even longer. Screening can obtain ultra fine particle size materials, and at this time, the productivity is the lowest.

6、 Installation and adjustment
The motor bracket of this machine is connected to the base frame with bolts. During installation, after leveling the frame, place the body of the grinder on the elastic support, and cross support the motor shaft and the machine spindle (exciter shaft) on the same centerline. Connect the flexible coupling.
Before starting up this machine, the following tasks must be done:
1. This machine should be installed on a solid and sturdy foundation. Fill the machine with abrasive media, and do not turn it on without abrasive media to prevent the machine from being too light and causing a car accident.
2. Connect the circulating water for cooling, which has two functions: first, to reduce the temperature of the bearings during operation and protect them; Secondly, for materials that cannot withstand high vibration and grinding temperatures, circulating water added to the outer jacket is used to absorb the heat generated during vibration and grinding in the vibration and grinding cylinder.
3. The motor power of this series of grinding machines is relatively high. It is recommended to use voltage reduction starting to reduce the impact on the power grid during startup. Generally, a dedicated starting motor cabinet is not configured. If there is a special need, it can be ordered separately. The electrical principle is shown in Figure 18-5.
4. If continuous automatic feeding and discharging are required, our factory can configure automatic feeding and discharging devices for users.
5. The required vibration grinding strength varies depending on the material used for vibration grinding. For this purpose, the secondary eccentric block can be increased or decreased. When a large excitation force is required, the secondary eccentric block can be bolted to the eccentric device. Conversely, the secondary eccentric block can be removed.
7. During installation, the different axial degrees of the motor shaft centerline should not exceed 2mm, which can be achieved by adding or removing adjustment pads and moving the motor seat.
8. Adjust the levelness of the grinder. Add adjustment pads under the spring base of the four support points to adjust the levelness of the grinding cylinder, with an allowable height difference of ± 3mm for unevenness. Move the lower support so that the spring has a different axis of 2mm between the upper and lower centers.
7、 Operation, use, maintenance and upkeep
1 Pre start inspection
(1) Is the power supply voltage normal;
(2) Whether the exciter rotates flexibly;
(3) Are there any foreign objects colliding with the vibrating body;
(4) Are all connecting bolts tightened;
(5) Are all supporting equipment such as feeders, conveyors, and circulating water in normal condition.
2 operate
(1) Open the cold water valve and introduce cooling water.
(2) Start the grinder and observe if it is functioning properly. If the motor cannot operate normally or the grinder vibrates abnormally after being powered on for 10 seconds, immediately press the stop button and check the cause.
3 Usage, maintenance and upkeep
(1) The direct water circulation liner of this series of mills has undergone a water pressure test after the equipment is manufactured. Before the user starts up, another water pressure test is required, with a water pressure of 0.2-0.3Mpa and no leakage.
(2) Before officially putting into operation, do not add any materials (but be sure to install abrasive media), conduct a two-hour air test run, check for accuracy, and then tighten all fasteners again.
(3) After starting up, the water temperature should be measured regularly from the outlet of the circulating cooling water, and the maximum water temperature should not exceed 40 ℃.
(4) The quality of bearing lubrication is one of the key factors affecting the performance of the grinding machine. Generally, high-temperature grease (such as heat-resistant grease produced by Yingkou Petrochemical Plant, numbered Liaoying Q327-82; 7016 high and low temperature grease and 7019 high temperature grease produced by Yiping Chemical Plant) should be added to the bearing chamber every 10-15 days. Open the bearing chamber every quarter, clean the bearings and bearing chamber, and during assembly, fill 40% -50% of the bearing space with high-temperature grease.
(5) To extend the service life of the lining, please change the direction of the drive motor every two months or so.
(6) The grinder needs to undergo a major overhaul once a year: 1. Replace the bearings; 2. Check the lining and various operating connections, and update them in a timely manner when necessary; Conduct pressure tests on three pairs of circulating water cooling systems, with a water pressure of 0.2-0.3Mpa and no water seepage.
8、 Explanation
(1) The lining material and grinding medium material used for materials with different requirements are different. To ensure the performance of the whole machine and the quality of the vibration grinding product, it is best to use specialized materials for the lining and grinding medium of the vibration grinder.
(2) The connection and discharge methods of the upper and lower cylinders can be flexibly changed according to needs.
9、 Precautions
(1) The connection between the eccentric block and the secondary eccentric block should be checked regularly to prevent damage and accidents caused by long-term use;
(2) Elastic supports should be regularly inspected and replaced, and unqualified elastic supports should never be used;
(3) Never turn on the device without sufficient media materials;
(4) Without a protective cover, it cannot be put into operation;
(5) Without cooling water, the startup time should not exceed 20 minutes;
(6) The strength of the flexible coupling connecting piece between the motor and the exciter cannot be arbitrarily increased;
(7) The inlet and outlet must be unobstructed, especially the outlet, and pipelines and devices that may affect the discharge cannot be connected externally;
(8) Without special protection, do not vibrate or grind flammable and explosive materials.
(9) The feeding must be uniform and continuous. The adjustment of its feeding amount is determined by the requirements of material properties and crushing ratio, while strictly controlling the entry of large blocks of materials.
(10) Before stopping the mill, stop feeding and continue running for 5 minutes before stopping the mill. After stopping for 8 minutes, turn off the circulating water to allow the bearings to cool down and avoid difficulties during the next start-up.
(11) Regular inspections and patrols should be carried out during work. If any abnormal sounds or other abnormal phenomena are found, the machine should be stopped immediately to check the cause, and the machine should be started after the fault is eliminated.
(12) The maximum temperature of the bearing seat during work should not exceed 65 ℃. If the temperature is too high, the cooling water supply should be increased or the water supply pressure should be increased to accelerate the circulation speed of the circulating water.
Welcome to Weicheng Machinery for inspection and guidance. We will provide shuttle services to the airport or train station. Contact: Manager Zhang Free Consultation Hotline:
Online inquiry