product details
Typical Process Flow Chart for Garbage Leachate Treatment
Process flow one |
Process flow 2
|
Process flow three
|
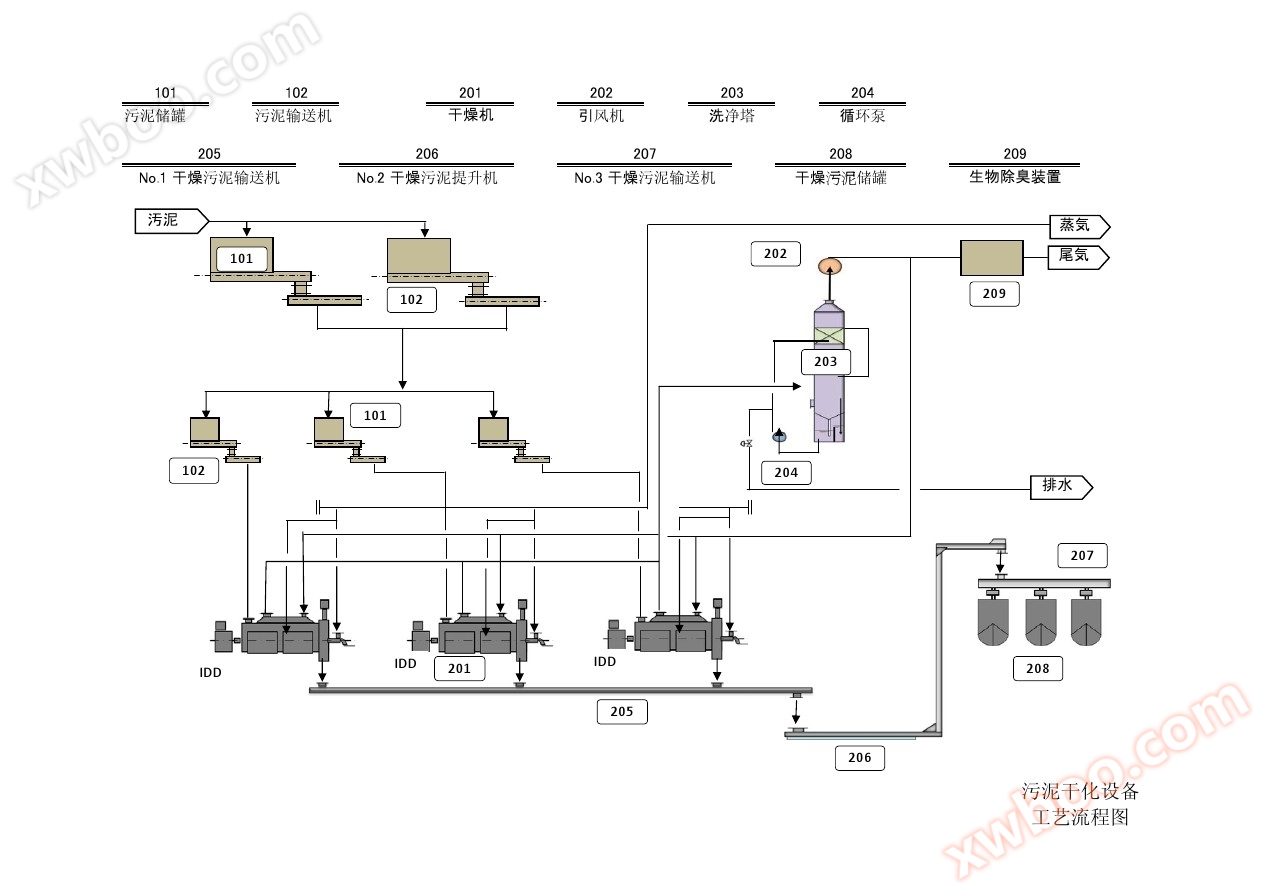
Introduction to Sludge Drying Machine Technology:
The earliest company in the world to use thermal drying technology for sludge treatment was Bradford in the UK. In 1910, the company first developed a rotary kiln sludge dryer and applied it to sludge drying practice. In the late 1980s, sludge drying technology gradually gained attention, and the application and promotion of sludge drying technology promoted changes in sludge treatment and disposal methods. This change was mainly reflected in the need to dry sludge before landfilling disposal; The proportion of sludge incineration disposal has been significantly increased; Dry sludge products are sold as fertilizer sources for land reuse, and the industry scale continues to expand. Nowadays, sludge drying treatment has also received increasing attention from the environmental engineering community, including developing countries.
In China, with the enhancement of national economic strength and the improvement of national environmental awareness, the urban sewage treatment industry has developed rapidly, and the production of urban sludge is increasing day by day. The disposal and development of sludge are increasingly concerned by people. The drying treatment of sludge makes it possible to use it for agricultural purposes, as fuel, incineration, and even to reduce landfill sites. The improvement and innovation of sludge drying technology have directly promoted the development of sludge disposal methods, expanded the selection range of sludge disposal methods, and provided increasingly reliable guarantees in terms of safety, reliability, sustainability, and other aspects.
The KJG series double axis hollow blade stirring dryer used by Changzhou Shengwanda Drying Equipment Co., Ltd. is an indirect heating, low-speed stirring drying equipment that uses saturated steam, hot water, or thermal oil as heating media. When using cooling media, it can be used for product cooling.
This type of equipment has been redesigned and applied in the field of sludge drying, and is currently one of the three mainstream equipment technologies in the world of sludge drying. The KJG series sludge dryer consists of two to four interlocked blade shafts, a W-shaped shell with a jacket, a machine base, and a transmission part. The entire drying process of sludge is carried out in a closed state, and organic volatile gases and odorous gases are sent to the exhaust gas treatment device in a closed atmosphere to avoid environmental pollution.
Sludge dryer is an indirect heating low-speed stirring dryer. There are two or four hollow rotating shafts inside the device, and fan-shaped wedge-shaped hollow blades are densely arranged in parallel on the hollow shafts, with a special and clever structural design. The relative rotation of the shaft body, utilizing the principle and structure of the same angular velocity but different linear velocity, cleverly achieves the self-cleaning effect of sludge on the shaft body, and maximizes the prevention of the "shaft hugging" phenomenon during the sludge drying process. Quickly flush the sludge through the "adhesive phase area" during the drying process at the fastest speed. Meanwhile, the clever structure enables the sludge to achieve a bi-directional shear state during the drying process. The dried sludge is quantitatively and continuously fed into the feeding port of the dryer by the screw feeder. The sludge enters behind the dryer and is flipped and stirred by the rotation of the blades, constantly updating the heating interface. It comes into contact with the body and blades and is fully heated, causing the surface moisture contained in the sludge to evaporate. At the same time, the sludge is transported in a spiral trajectory towards the discharge port by the rotation of the blade shaft, and continues to stir during transportation to evaporate the water seeping out of the sludge. Finally, the uniformly dried qualified products are discharged from the discharge outlet. Adopting a jacket type shell structure, the sludge is uniformly heated at various interfaces inside the machine. The shaft rotates, and the sludge continuously churns inside the equipment, while the heating surface is constantly renovated. This greatly improves the steaming efficiency of the equipment, achieving both the purpose of sludge drying and the low-cost operation of the entire system.
Process technical specifications
1. Source of Sludge: Municipal Sludge Factory Sludge Electroplating Sludge Printing and Dyeing Sludge Domestic Sludge
2. Fully dried: The moisture content of the incoming mud is 80-85% (wet basis), and the moisture content after drying is 10% (wet basis)
3. Semi drying: The moisture content of the incoming mud is 80-85% (wet basis), and the moisture content after drying is 40% (wet basis)
Equipment features
1. Energy saving: Energy saving is the biggest advantage of this equipment, which ensures the low-cost operation of the complete set of equipment by reducing energy consumption;
2. Intensive processing: A single machine can process up to 100 tons of sludge per day, making the entire equipment intensive;
3. Environmentally friendly: All system equipment operates in a sealed manner, with no dust or odor leakage. The complete set of equipment operates under negative pressure,
The site is clean and hygienic, with good environmental performance;
4. Intelligence: All system equipment adopts intelligent detection, automatic control and manual control of two lines, which is more conducive to production
On site stabilization operations;
5. Simplification: Due to the clever structure of the equipment and the idea of breaking it down into smaller parts, it is beneficial for the maintenance and repair of the equipment,
Not only does it reduce the labor intensity of production workers, but it also lowers the higher demand for on-site maintenance equipment
The level requirements are more suitable for the needs of usage and production practices in developing regions.
Equipment processing capability
Wet mud processing capacity specifications: 10 tons/day, 20 tons/day, 30-35 tons/day, 50-60 tons/day, 80 tons/day, 100-120 tons/day
The value of sludge drying
edit