Water treatment equipment needs to almost completely remove conductive media from water, as well as remove colloidal substances, gases, and organic matter that do not dissociate from water to a very low level. The resistivity is about 10-18.3M Ω. cm, the limit value. Ultra pure water is a level that is difficult for general pure water equipment to achieve. It usually involves four steps: pretreatment, reverse osmosis technology, high purification treatment, and post-treatment. Multiple treatment methods such as multi-stage filtration, high-performance ion exchange (polishing), ultrafiltration filter, ultraviolet lamp, and TOC removal device are used to achieve a resistivity of up to 18.25M Ω· cm.
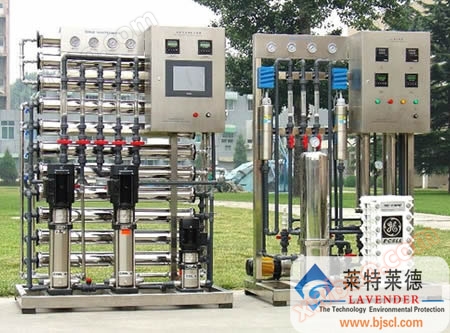
Application areas:
In recent years, electrodeionization has been increasingly valued in various industrial fields, and many industrial systems have begun to adopt electrodeionization as a replacement technology for their water treatment systems, such as the power industry, pharmaceutical industry, microelectronics industry, electroplating, and metal surface treatment.
Water quality: 0.5M Ω· cm, 2M Ω· cm, 10M Ω· cm, 15M Ω· cm, 18M Ω· cm
Usage: Ultra pure water quality is divided into five industry standards, namely 18M Ω· cm, 15M Ω· cm, 10M Ω· cm, 2M Ω· cm, and 0.5M Ω· cm, to distinguish different water qualities.
(1) Electric power industry
It is estimated that the operating cost of water treatment units in the power industry accounts for about 10% of the electricity cost, and replacing ion exchange resin with electrodeionization can reduce the cost of treating 1000 gallons of water from $11 to $1.75.
(2) Pharmaceutical industry
Although the characteristic of medicinal water is that it does not require a high degree of deionization, the electro deionization system has the ability to simultaneously remove salt and control microbial indicators. Therefore, many companies have adopted RO/EDI integrated systems. It is said that this type of system has stable performance, continuous computer monitoring throughout the entire process, and fully automated operation without human supervision.
(3) Electronic industry
The electronic industry has extremely high requirements for water quality, with a stable water resistance rate greater than 18M Ω, while EDI effluent is generally around 15-17 M Ω. Therefore, in the production process of electronic grade water, EDI+polishing resin system is often used, which adds ion exchange after EDI. Although ion exchange is still required in this project, because EDI has removed most of the ions, polishing resin hardly needs to be regenerated, so the water treatment cost is still very low.
(4) Electroplating and Metal Surface Treatment
Electrodeionization can be used for electroplating wastewater treatment to reuse water and recover heavy metal ions. The United States already has experimental facilities for this type of system.
(5) Other fields
Electrodeionization has a wide range of applications in the food industry, chemical industry, etc.: multi chamber fluidized beds and equipment with rectangular cross-sections are generally divided into multiple chambers (usually 4-8 chambers) along the length direction by vertical baffles. There is a gap of several tens of millimeters between the lower edge of the baffle and the distribution plate surface, which serves as a passage for inter chamber powder particles. The fluid enters each chamber in parallel, while the particles pass through each chamber in sequence. Therefore, a multi chamber fluidized bed can not only suppress particle backmixing throughout the entire bed, but also regulate the flow rate and temperature of the fluid entering each chamber. Multi chamber fluidized bed equipment is easier to control and has a lower total pressure drop compared to multi-layer fluidized bed equipment; However, the driving force for heat and mass transfer is smaller than that of multi-layer beds, and the utilization efficiency of air heat during drying is relatively poor. There are two fluidized beds in the two fluidized beds, with fluidization on the left side.
Process flow:
1. The process of using ion exchange is as follows:
Raw water → raw water booster pump → multi-media filter → activated carbon filter → water softener → precision filter → cation resin filter bed → anion resin filter bed → anion resin mixed bed → microporous filter → water point
2. Adopting a two-stage reverse osmosis method, the process is as follows:
Raw water → Raw water booster pump → Multi medium filter → Activated carbon filter → Softener → Precision filter → First stage reverse osmosis → PH adjustment → Intermediate water tank → Second stage reverse osmosis (with positive charge on the surface of the reverse osmosis membrane) → Purified water tank → Pure water pump → Microporous filter → Water point
3. The process of using EDI is as follows:
Raw water → Raw water booster pump → Multi medium filter → Activated carbon filter → Softener → Precision filter → Primary reverse osmosis machine → Intermediate water tank → Intermediate water pump → EDI system → Microporous filter → Water point