Classification of sub high efficiency filtersHigh temperature resistant sub high efficiency filter, combined sub high efficiency filter;
The sub high efficiency filter uses ultra-fine glass fiber filter paper or polypropylene filter paper as the filter material, which is densely folded. The filter paper of the ultra-high efficiency filter is separated by small inserts made of paper or aluminum foil partitions to maintain a smooth passage. The outer frame is made of galvanized sheet, stainless steel sheet or aluminum alloy profile, sealed with a new type of polyurethane sealant.
Sub high efficiency filters can be widely used for general filtration in industries such as electronics, pharmaceuticals, hospitals, and food, and can also be used in high-temperature resistant places.
The non partition sub high efficiency filter uses ultra-fine glass fiber filter paper or polypropylene filter paper as the filter material, separated by hot melt adhesive, and the outer frame is made of cardboard, aluminum alloy profile or galvanized sheet, sealed with environmentally friendly polyurethane sealant.
Sub high efficiency filters are generally used in semiconductor manufacturing plants, atomic force research centers, clean rooms, laminar flow equipment, workbenches, and other places that require ultra-high cleanliness.

Characteristics of sub high efficiency filters:
1. The unique seamless sealing technology of the sub high efficiency filter provides better sealing effect, longer durability, and less leakage;
2. Sub efficient filter material with double-sided metal mesh protection;
3. The sub high efficiency filter can provide various thicknesses such as 50mm, 69mm, 90mm, etc;
4. Scanning and counting MPPS efficiency per laser: 95% -99.95% (EN1882);
5. Filtering grade: H10-H12 (EN1882).

Classification of sub high efficiency filters:
Sub high efficiency filters are divided into partitioned sub high efficiency filters and non partitioned sub high efficiency filters:
Divided sub high efficiency filters including GK(Sub high efficiency filter with partition)GKW (high temperature and sub high efficiency filter), GKA (high humidity and sub high efficiency filter);
Non partition sub high efficiency filterIncluding GKYW (combination type sub high efficiency filter), GKYS (non partition sub high efficiency filter), GKYC (liquid tank type sub high efficiency filter), GKYL (ultra-low resistance non partition sub high efficiency filter), GKYD (knife holder type non partition sub high efficiency filter).

Specifications, dimensions, and technical parameters of sub high efficiency filters:

The filtering object of the sub high efficiency air filter is dust particles with a diameter of 1-5 μ m. The filter material is generally made of glass fiber paper, ultra-fine polypropylene fiber paper, etc. Its structural types include thin plate type, partition plate frame type, and wedge-shaped structure. The series and models of high-efficiency air filters include YGK series, GZH series, YL series, HDQYB type, HDQYE type, and HDQYK type.
The main control parameters selected for the sub high efficiency air filter include filtration efficiency, rated air volume, initial resistance at rated air volume, dust holding capacity, and external dimensions. Avoid installing the sub high efficiency filter directly on the downwind side of the shower room or humidifier. Effective measures should be taken when it is impossible to avoid it.

Key points for selecting sub high efficiency filters:
1. The main control parameters for selecting sub high efficiency air filter products include filtration efficiency, rated air volume, initial resistance at rated air volume, dust holding capacity, and external dimensions.
2. According to the method specified in JG/T22-1999 "Performance Test Method for Air Filters for General Ventilation", filters with an atmospheric dust counting efficiency of ≥ 95% and<99.9% for particles with a particle size of ≥ 0.5 μ m are considered sub high efficiency air filters.
3. Common filter materials for high-efficiency air filters include polypropylene.
4. The manufacturer should provide the dust holding capacity of the filter.
5. The initial resistance of the sub high efficiency air filter should be ≤ 120Pa. During design, the final resistance can be calculated as twice the initial resistance of the filter.
6. The air filter should meet the fire prevention requirements, and the flash point of the coating of the air filter should not be lower than 163 ℃.
7. Sub high efficiency air filters should not be used independently, but should be combined with coarse and medium efficiency air filters.
8. Generally used as the end filter for lower level clean air conditioners.

Execution standard for sub high efficiency filters:
Product standards
GB/T14295-93 "Air Filters"
JG/T22-1999 "Performance Test Method for Air Filters for General Ventilation"
Engineering standards
GB50073-2001 "Code for Design of Cleanrooms"
GB50333-2002 "Technical Code for Building of Hospital Clean Operating Department"
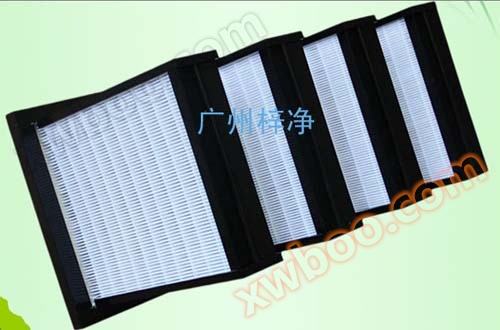
Selection criteria for sub high efficiency filters:
1. Mainly considering factors such as filtration efficiency, rated air volume, initial resistance, and dust holding capacity;
2. The commonly used filter materials for high-efficiency air filters include ultrafine glass fibers, etc;
3. When selecting, it should comply with the standards for preventing * * *;
4. When designing, the final resistance can be twice the initial resistance;
5. The initial resistance of the equipment cannot exceed 10% of the resistance of the product sample;
6. High efficiency air filters must not be used alone and must be installed at the end of the purification air conditioning system;
7. In ordinary non parallel flow clean air conditioning systems, combined filter vents are generally used.
Requirements for after-sales service time of purification equipment:
Whether it is paid after-sales service or free after-sales service, customers provide feedback to our company regarding equipment after-sales issues. After our company provides a solution and the customer confirms the solution:
1. Arrive at the site within 24 hours within the Pearl River Delta and Yangtze River Delta to solve after-sales service problems;
2. In other areas, it is generally within 48 hours to arrive on-site to solve after-sales service problems, while in special remote areas, it is up to 96 hours to arrive on-site to solve after-sales service problems.
Original source: Guangzhou Zijing http://www.zj-filter.com/ Li Gong (139-2875-8616)